新房装修前究竟要不要请看风水呢
- 作者: 刘嘉映
- 来源: 投稿
- 2024-11-10
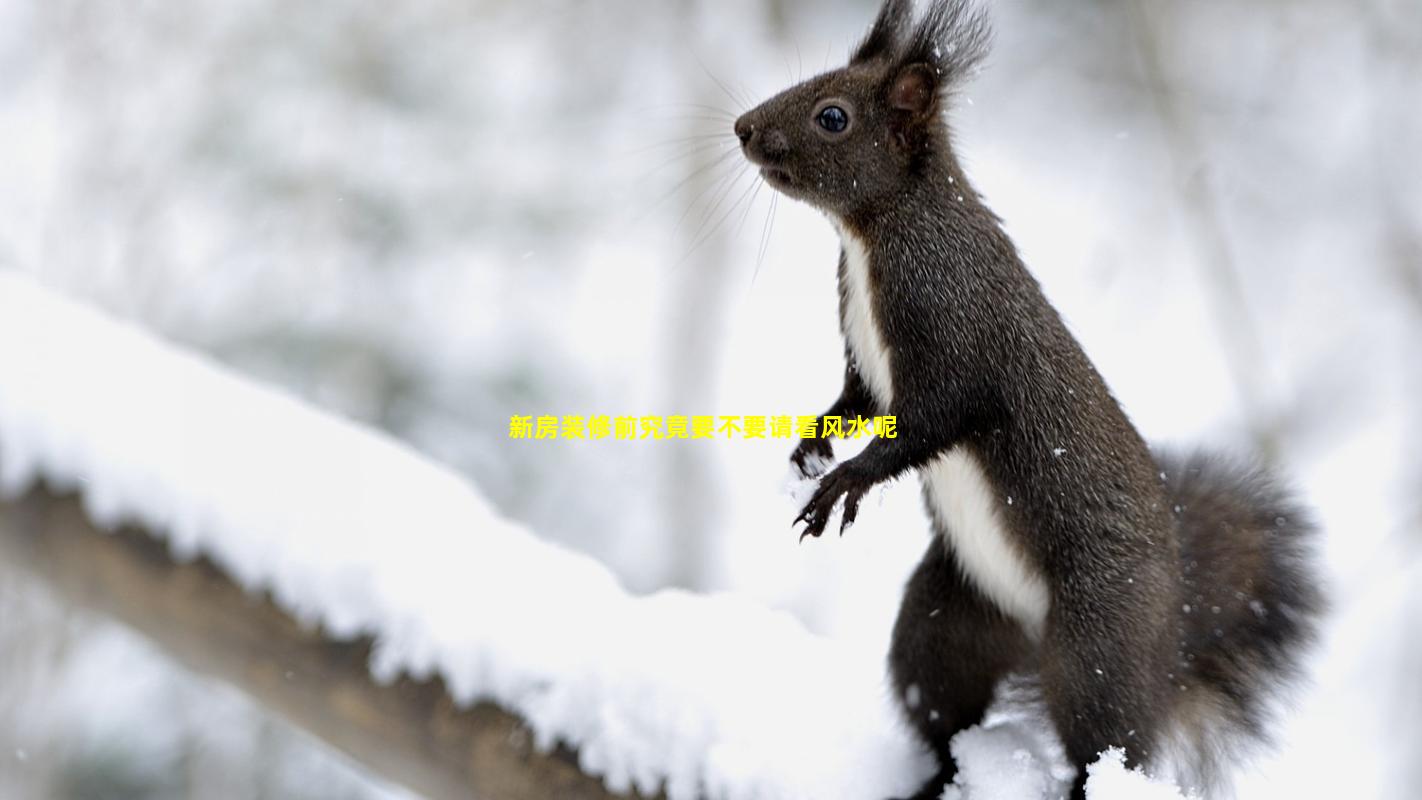
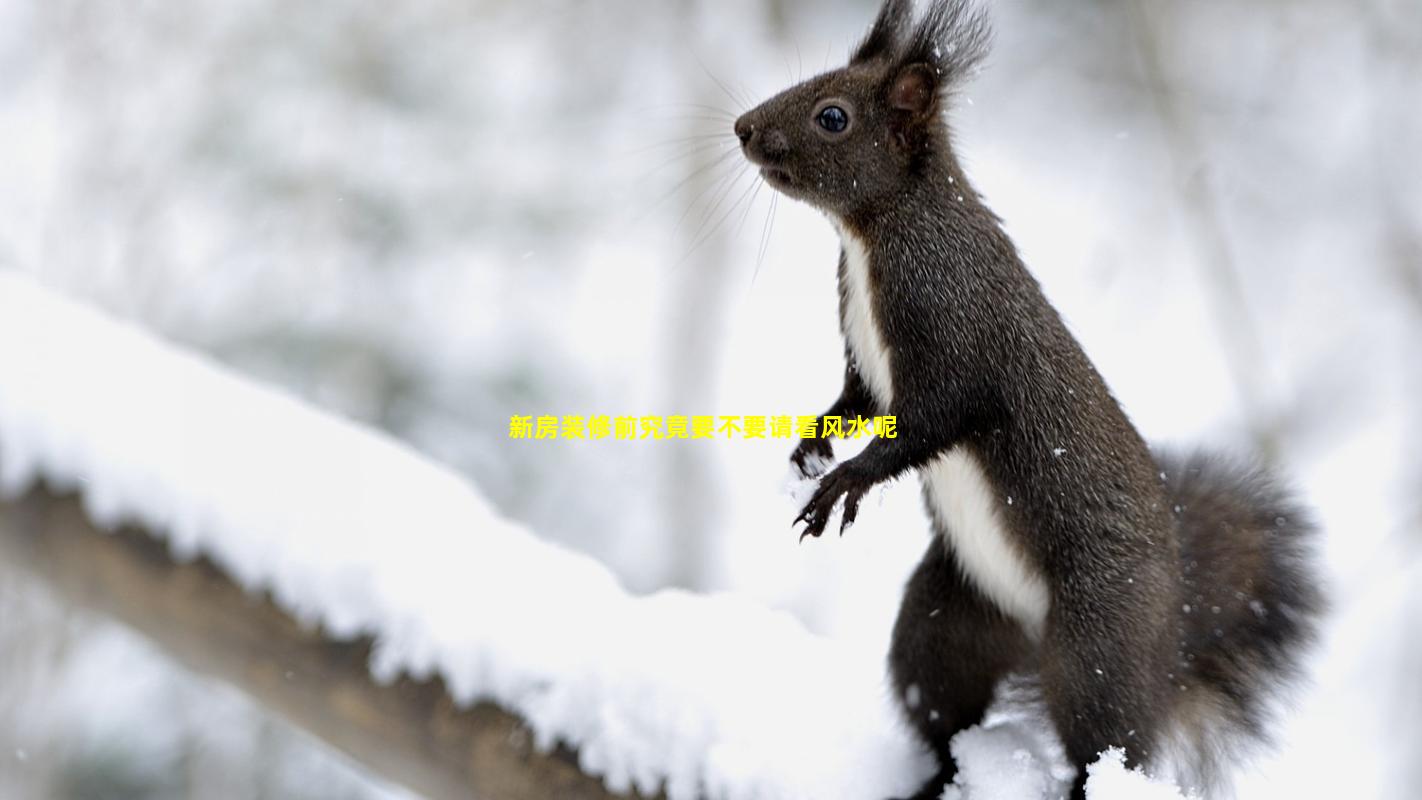
1、新房装修前究竟要不要请看风水呢
新房装修前请看风水是否有必要,取决于个人的信仰和重视程度:
正方观点:文化传承:风水在中国文化中根深蒂固,许多人认为遵循风水有助于带来好运和吉祥。
心理安慰:看风水可以缓解装修过程中的压力和焦虑,让人感到 安心和有保障。
家居舒适度:风水注重空间布局、采光通风等因素,有利于营造舒适居住环境。
增值潜力:据说风水良好的房子更有助于升值,吸引买家。
反方观点:迷信色彩:风水理论存在争议,缺乏科学依据。
主观性强:风水大师的看法往往主观性强,不同大师给出的建议可能差异较大。
经济成本:请看风水需要支付一定费用,对于经济条件有限的人来说是一笔额外开支。
影响装修设计:遵循风水建议可能会限制装修设计选择,影响个人审美和喜好。
建议:尊重个人信仰:如果本人或家人对风水有信仰,建议考虑请看风水。
权衡利弊:在决定是否请看风水之前,综合考虑以上的正反观点,权衡利弊。
选择专业人士:如果决定请看风水,应选择经验丰富、信誉良好的风水大师。
不必盲从:即使请了看风水,也不必完全照搬风水建议,可以结合自己的实际情况和喜好进行取舍。
适度即可:过于迷信风水可能会造成心理负担,适度考虑风水即可。
最终,是否请看风水是一个个人决定。尊重自己的信仰和重视程度,做出最适合自己的选择即可。